
Anwendung eines neuen Vanadium-Rückgewinnungsharzes und einer automatischen Steuerungstechnologie bei der Vanadiumrückgewinnung aus Steinkohle
Steinkohle ist ein Sedimentgestein, das zwar wie Stein aussieht, aber nach komplexen biochemischen und physikochemischen Reaktionen unter reduzierenden Bedingungen der Überreste niederer Organismen (Algen, Pilze und Plankton), die sich im frühen Paläozoikum in großen Mengen vermehrten, zur Kohleverbrennung verwendet werden kann. Steinkohle kann je nach physikalischer Form in drei Arten unterteilt werden: Massivkohle, Pulverkohle und Bänderkohle. Derzeit wird hauptsächlich Massivkohle abgebaut und verwendet.
Viele Metalle wie V, Mo, Ni, U, Ga, Cu, Cr, insbesondere V2O5, sind häufig in Steinkohle enthalten. Der V2O5-Gehalt kann in manchen Minen durchschnittlich 0,4–1,0 % erreichen, in anderen sogar 2 % oder sogar 3,7 %. Nach der Behandlung des vanadiumreichen Erzes durch Oxidationsröstung, Säurelaugung und andere Verfahren kann Vanadium gewonnen werden. Die Industrie zur Vanadiumgewinnung aus Steinkohle entwickelt sich mit der Zeit.
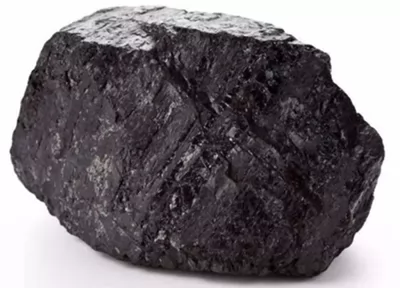
Zurzeit gibt es zwei industrielle Verfahren zur Gewinnung von Vanadium aus Steinkohle: die Säurelaugung und
Ionenaustausch
Beim Säurelaugungs- und Extraktionsverfahren wird vanadiumhaltiges Gestein nach Grob- und Feinzerkleinerung, Sieben und Mahlen über einen längeren Zeitraum mit hochkonzentrierter Säure bei hoher Temperatur extrahiert und anschließend mit P2O4 und 99,9%iger Schwefelsäure extrahiert. Die Extraktionsrate kann 97–98 % erreichen. Allerdings stellt der Extraktionsprozess hohe Anforderungen an den Korrosionsschutz der Geräte, erfordert große Anlagen und hohe Investitionen in die Geräte. Durch die Einführung eines Extraktionssystems werden die Unternehmen stärker in Bezug auf Sicherheit und Umweltschutz belastet. Der Betrieb der Systeme verbraucht viel Säure und bei der Vanadiumfällung entstehen große Mengen Ammoniumsalze, was die Abwasserbehandlung belastet. Beim Ionenaustauschverfahren der Säurelaugung wird das Vanadium im Erz durch Rösten und Säurelaugung in wasserlösliche Vanadiumionen umgewandelt. Anschließend wird das Vanadium im Lösungssystem selektiv ausgetauscht, indem je nach Ionenform ein geeignetes Ionenaustauscherharz ausgewählt wird.
Im Vergleich zum Extraktionsverfahren ist der Ionenaustauschprozess einfacher in der Handhabung und kleiner im Maßstab. Zudem ist er aufgrund der Verwendung von Extraktionsmittel nicht mit Sicherheits- und Umweltschutzauflagen konfrontiert. Er hat sich in der Industrie zum bevorzugten Verfahren entwickelt. Die konventionelle
Anionenaustauscherharze
Die in der Industrie üblicherweise zur Vanadiumextraktion aus Steinkohle mittels Ionenaustauschverfahren eingesetzten Harze führen zu Problemen wie geringer Adsorptionskapazität, mangelhafter Adsorptionsgenauigkeit und häufiger Regeneration, was wiederum hohe Kosten für die Vanadiumextraktion verursacht. Daher erwartet die Industrie die Einführung eines neuen Vanadiumextraktionsharzes mit größerer Adsorptionskapazität, besserer Adsorptionsgenauigkeit und längerer Haltbarkeit.
Sonnenharz
hat eine neue
Vanadium-Extraktionsharz
basierend auf eigener Erfahrung und Technologie in der Harzforschung und -entwicklung sowie der Optimierung von Anwendungsprozessen. Nach industrieller Überprüfung verfügt das Harz im Vergleich zu herkömmlichen Anionenaustauscherharzen über eine höhere Adsorptionskapazität und -festigkeit, eine bessere Selektivität für fünfwertiges Vanadium und eine hervorragendere Anti-Schmutz-Wirkung und wird von industriellen Produktionsunternehmen gut angenommen.
Vorteile des Spezialharzes von Sunresin zur Vanadiumextraktion:
1) Das Harz hat eine höhere Austauschkapazität und kann mehr verarbeiten.
2) Die mechanische Festigkeit des Harzes ist besser, der Schadensverlust während des Betriebs ist geringer und der jährliche Ergänzungsbetrag ist niedriger.
3) Das Harz verfügt über eine hervorragendere Anti-Verschmutzungsfähigkeit, eine hohe Adsorptionspräzision und eine bessere Selektivität für Vanadium.
4) Das Harz hat eine lange Lebensdauer.
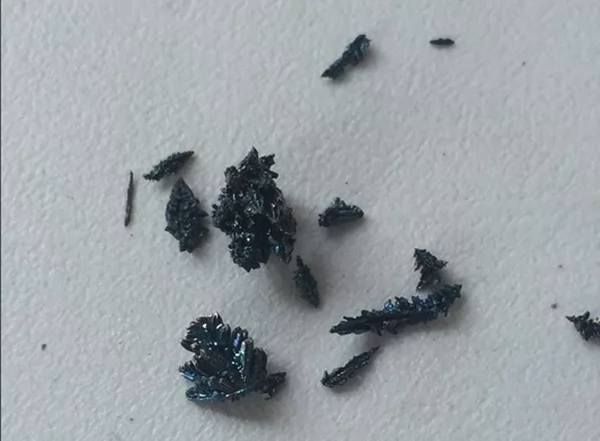
Gleichzeitig führte Sunresin in Kombination mit einem spezifischen Produktionsprozess eine fortschrittliche automatische Steuerungstechnologie und ein effizientes Harztrenn- und -reinigungssystem in den industriellen Betrieb der Vanadiumextraktion aus Steinkohle ein, um die Betriebseffizienz des Systems zu verbessern und die Entwicklung und Verbesserung des Ionenaustauschprozesses der Vanadiumextraktion aus Steinkohle zu fördern.
Die Vorteile des Sunresin-Verfahrens bei der Vanadiumgewinnung:
1) Zufuhr, Säurezufuhr und Alkalizufuhr werden durch Frequenzumwandlungspumpe, Dosierpumpe, Regelventil usw. präzise gesteuert. Die Steuerung der Prozessparameter ist genauer. Der Produktionsprozess ist kompakter und der Einfluss menschlicher Faktoren wird reduziert.
2) Durch das automatische Steuerungsprogramm kann der Produktionsprozess jederzeit überwacht werden, um den Betriebsstatus des Harzes und jeden Prozessstatus zu verstehen und so eine Echtzeitüberwachung und -verwaltung des Produktionsprozesses zu realisieren.
3) Die Steuerplattform kann mit der Hauptsteuerung verbunden werden, und die Betriebsparameter können jederzeit entsprechend den Anforderungen angepasst werden. Das ungestörte Umschalten zwischen manueller und automatischer Steuerung ist möglich, und die Bedienung ist komfortabler.
4) Tankfüllstand, Säure- und Laugenvorbereitung, Temperaturregelung usw. können eine automatische Überwachung und Regelung realisieren und die Stabilität und Zuverlässigkeit des Systems verbessern.
Sunresin wird sich weiterhin intensiv mit der Harzentwicklung und innovativen Anwendungstechnologien im Bereich der Hydrometallurgie befassen und die Bedürfnisse der Anwender frühzeitig erkennen. Sunresin wird mit seiner Professionalität, seinem pragmatischen Denken und seiner aufmerksamen Serviceorientierung voranschreiten, Industrieunternehmen bessere Problemlösungen bieten und die metallurgische Industrie mit seiner Stärke unterstützen.